Umm Al Houl Power, one of the largest independent water and power plants in Qatar and the Middle East, is driving innovation in Qatar’s utilities sector with increased efficiency in management of its business processes and resource utilisation, thanks to a digital transformation partnership with SAP.
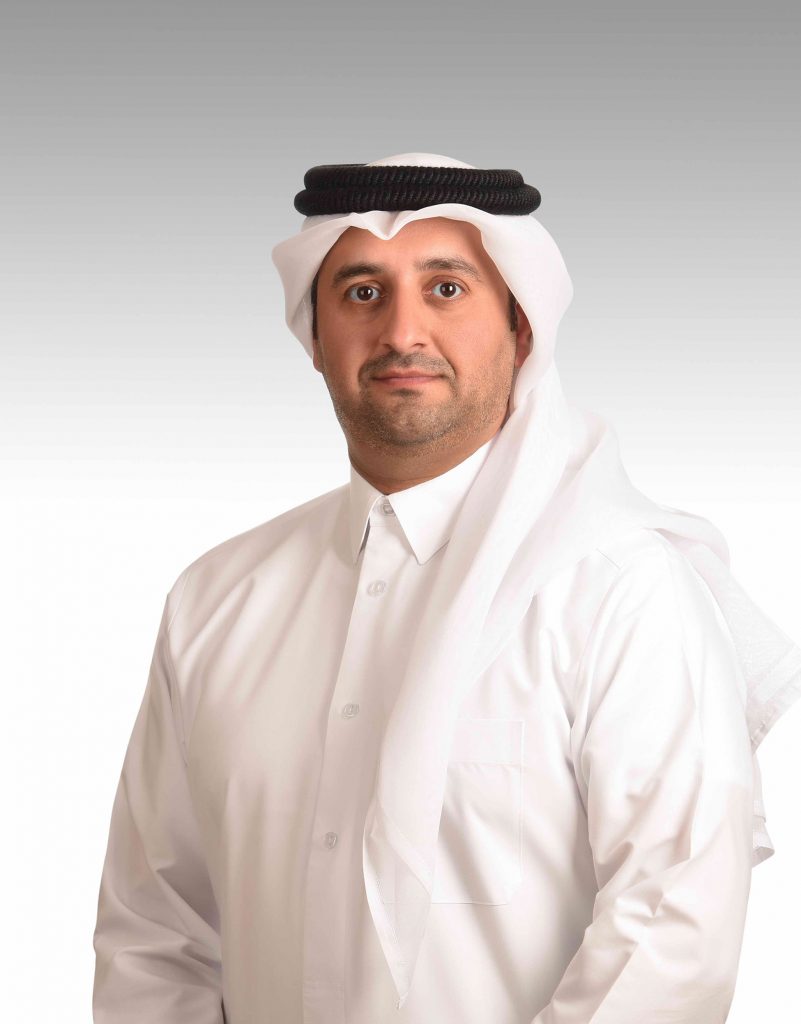
In its digital transformation, Umm Al Houl Power has worked with the channel partner Kaar Technologies LLC to deploy a wide range of real-time business solutions that are enabling a paperless office.
“In line with Umm Al Houl Power’s goals of providing a secure power and water supply, we needed full visibility on our utilities operations and resources,” said Khaled Al Siddiqi, Business Manager, who leads the Digital Transformation initiative at Umm Al Houl Power. “UHP is one of the Best Run Utility, with a highly skilled, lean and efficient organisation structure we have achieved an annual Revenue to Employee ratio of more than USD 3 million per employee – which is one of the highest in the world for any sector.”
Khaled Al Siddiqi said, “We have been able to manage this amazing feat by providing our employees with advanced technological tools that ensure right actions at the right time and at the right cost. Very early on we took the very important decision to digitally transform our company across the board, be it our Human Resource Management, Operation, and Maintenance Management, Material Resource Management, or Financial Accounting and Cost Management.
“Thanks to our digital transformation with SAP, we’ve seamlessly integrated data from our plant OT into SAP MII to provide real time KPIs and Dashboards for effective Management oversight, data from the DCS and field operators and technicians is routed directly to the concerned engineers for real-time decision-making, this has led to new levels of employee productivity.
“Through the Digital Planning Board engineers can assign the right resources at the right price and right time. Technicians can access assigned job orders, technical documents, permits, check, and call in physical inventory through SAP MM module on their mobile devices to quickly diagnose and fix any issues without any administrative delays. Our implementation of ESS and MSS with SAP Fiori on mobile has almost eliminated any lag time by enabling requests and approvals on the go. With continuous collaboration with SAP and our policy to leverage innovative technologies, I am confident Umm Al Houl Power can keep our operations running at maximum efficiency into the future,” said Khaled Al Siddiqi.
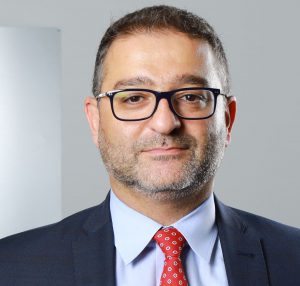
Now, Umm Al Houl Power has granular data on one real-time platform, delivering unprecedented analytics, efficiency, and productivity. The company has less asset downtime, and spends less time and effort on routine administrative tasks with more time used for strategic planning. UHP is currently implementing SAP Ariba, digitally enabling the complete procure to pay cycle, which is expected to further optimise Capex.
In the future, Umm Al Houl plans to use real-time solutions like field-based equipment integrated with mobile devices, artificial intelligence, machine learning, and robotic process automation for predictive maintenance of its assets, which could further optimise costs and efficiency.
“In the Middle East’s highly competitive utilities sector, Umm Al Houl Power demonstrates the power of digitally transforming into an Intelligent Enterprise,” said Mazen Raad, Managing Director, SAP Qatar. “By using real-time solutions, Umm Al Houl Power has optimised its utilties scheduling, resources, and supply chain of their spare parts – optimising operations and customer experiences.”
Umm Al Houl Power is a Joint Venture Company with the Qatar Electricity and Water Company, Qatar Petroleum, Qatar Foundation, and Japan’s K1 Energy that is comprised of Mitsubishi and Jera.
Discussion about this post