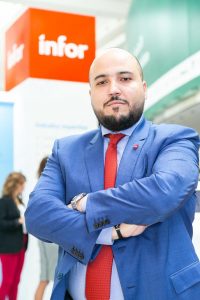
Against the backdrop of an increasingly uncertain global economy, one area of consistent investment has been digital transformation. Within manufacturing, that means the ongoing evolution towards Industry 4.0.
The rationale is simple enough. Manufacturers that are willing to embrace Industry 4.0 connectivity and modern automation opportunities stand to see significant improvements in productivity—not only on the shop floor, but also across the enterprise.
Another reason that these programmes are still being developed is because they can engender a great deal of confidence amidst volatile markets. Industry 4.0 improvements are all very tangible and quickly identified and measured. According to a joint survey on smart factories from PwC and the Manufacturing Institute, productivity gains, reduced labour costs, and uncovering new revenue streams are among the top benefits for manufacturers that have deployed Industry 4.0 technologies.
This confidence is so strong that while many manufacturers are still in the research and pilot stages, the survey reports that 73% of them are planning to increase their technology investments over the next year. But where exactly should manufacturers look to secure these early wins and focus their investment plans to deliver not only resilience but growth?
- Shop-floor optimisation
Manufacturers can use Industry 4.0-ready technologies to help digitise shop floor processes that are still largely paper-based. Today, many manufacturers still use paper trails to monitor the progress of work orders, the location of parts, and sometimes even the assembly sequence and steps for a specific order. This is not only inefficient in the immediate, ‘here and now’ but it restricts the speed and agility that is vital for new product development to help drive the future growth of a manufacturer.
Modern software provides ways to automate and streamline steps as new functionality anticipates the needs of the user, based on roles and custom-defined workflows. Modern software empowers faster decision-making with easy-to-read dashboards, workbenches, and consumable reporting.
- Transparent supply chain
Efficiently filling customer orders is top of mind for manufacturers. According to a survey from industry advisory firm BDO, 23% of midmarket manufacturers are looking to supply chain technologies to help speed up order cycle times.
In an age where we can track every personal delivery to our home, businesses (including manufacturers) now realise that they need end-to-end supply chain technologies that give them a network-wide view of inventory on order, so they can see where potential bottlenecks may be—whether it’s from the supplier during transport, or once it makes it to the manufacturing facility.
- Workforce augmentation
Automation often strikes a note of fear into many manufacturers, but collaborative robots, or “cobots,” aren’t here to replace human workers, but to work side-by-side with them to help handle the heavy work or repetitive tasks that can be hard on employees’ bodies over time.
With cobots taking on some of the more monotonous tasks, human employees can focus on activities that require more dexterity, creativity, reasoning, and critical thinking.
This has the potential to be truly transformative over the long term.
Just as robots can help on the shop floor, workforce management and human capital management systems can help a manufacturer’s employees succeed as the roles and responsibilities within the workplace shift. These software tools can provide ease of use, automation, and analytics that help managers plan the use of resources and control labour costs, while also enhancing the employee experience.
- Predictive asset maintenance
It’s mission-critical for shop floor equipment and assets to keep running—even when the machinery is past its prime and needs frequent repairs or even replacement. With minimal resources and numerous demands for their time, maintenance teams need to develop and follow optimal strategies.
Reactive maintenance isn’t an acceptable strategy—fixing broken equipment, one emergency after another, is an inefficient use of resources and can even result in entire production lines shutting down. A predictive maintenance strategy, however, can catch issues before they become expensive and time-consuming problems.
Modern enterprise asset management software systems contain powerful predictive capabilities combined with innovative business intelligence and artificial intelligence that uses algorithms and data science to identify patterns in data points and project next-likely outcomes. Users can explore “what if” scenarios and obtain forecasts of likely costs and probable demands to help drive decision-making.
It is worth concluding on a note of realism. Industry 4.0 is not a panacea for the current issues impacting global manufacturing – it wasn’t before COVID19 hit and it still isn’t now. But it is a set of tools that can not only improve the response to issues such as economic difficulties imposed by the coronavirus, but also drive future growth and strength within the sector.
As an example of digital transformation, Industry 4.0 can lead a lot of businesses forward, but early wins will be critical to maintain confidence and investment levels, helping businesses to realise positive initial progress and develop competitive advantage.
Discussion about this post